Having an entry to your basement that’s located outside your home can come in handy. Being able to get straight from the yard to your storage space or workshop can save trailing dirty equipment through your nice clean home. On the flipside, they are also effectively a hole in your basement wall that leads directly to where the weather is. This means that leaking basement bulkheads are an all too common occurrence. Luckily, there’s a whole host of methods for bulkhead waterproofing that can make your leaking basement bulkhead a thing of the past.
Types Of Bulkhead Foundations
There is more than one type of bulkhead door common across the US. Which style you have can have an influence on how and why the water is finding its way through.
Precast Concrete Bulkheads
Precast bulkheads are a common sight, thanks to their durability. They consist of precast sections which can be joined on to a foundation wall, allowing a sturdy entrance to a basement space. This makes them incredibly versatile and easy to install.
Unfortunately, they do come with two distinct downsides.
- The joint between the precast section and the foundation wall can be a weak spot and prone to water leakage.
- It’s hard to properly compact the earth around the lowest sections thanks to the shape. This means that groundwater can often pool here and work its way through the concrete.
Cinderblock Bulkheads
Another common choice for bulkhead design is cinderblock. They’re lightweight and cost effective. While poured concrete is generally more popular today, there are still plenty of blockwork basement bulkheads out there.
Cinderblocks come with a few drawbacks when used at ground level. They’re prone to cracking under stress and their joints can be particularly susceptible to seepage.
Poured Concrete Bulkheads
Poured concrete is the go-to choice for most modern buildings. It’s strong, seamless and relatively easy to waterproof. Adding a bulkhead door is a relatively easy addition and carries the same benefits as a poured concrete foundation.
On the negative side, a poured concrete bulkhead also has the same vulnerabilities as any other concrete. It can be prone to cracking, creating easy pathways for water to enter your home.
Understanding the Causes of a Leaking Basement Bulkhead
A leaking basement bulkhead could be down to issues with the construction, age, damage from general wear and tear or the foundation walls settling.
Cracks in Key Areas
While concrete is pretty sturdy stuff, it’s not invulnerable to damage. Cracks can form for all kinds of reasons but the most common causes in bulkheads are simply age related wear and tear or the structure settling into the foundations.
The most common areas to find these cracks varies by construction type. Precast bulkheads are prone to cracking around the place where they join the basement whereas cinderblocks can suffer from joint erosion.
Regardless of the exact reasons, the result is the same: an easy path for water to find its way through.
Aging or Poor Installation
Concrete lasts a long time but, like everything else, time will eventually take its toll. Likewise, the doors themselves will eventually rust, corrode, warp or otherwise degrade (depending on the materials they’re made of). Even the rubber gaskets which are meant to create a watertight seal around the doors will eventually perish. The result of the aging process is gaps forming and water getting through.
Even in newer builds, poor installations can lead to these gaps forming. A badly executed seal between the bulkhead and the foundation wall or the door can exacerbate leakage issues and let the water in.
Gaps and Seals
Given time and pressure, even well installed bulkhead seals will eventually give way and allow water through. These joints are a weak spot and vulnerable to failure regardless of the build type or materials used.
Material Specific Vulnerabilities
Each style of bulkhead comes with its own set of vulnerabilities:
- Precast Bulkheads: The joints between the bulkhead and foundation can often allow water to seep through. This problem becomes more and more likely as the joints age.
- Cinderblock Bulkheads: Mortar joints between the blocks can weaken, come loose or even erode. When this happens, they create an easy pathway for water to flow through.
- Poured Concrete Bulkheads: Small cracks (even microscopic pores in the concrete) can allow water through. Over time, these can widen allowing more and more to enter your basement.
Improper Grading and Drainage
Grading is the process of ensuring that the ground slopes away from your foundation walls. Water will always flow downhill, so the idea is that proper grading makes water pooling against your home all but impossible. If this hasn’t been done properly, there’s a risk that water will pool around your basement bulkhead.
Likewise, poor drainage can exacerbate other vulnerabilities. The longer water sits against the bulkhead, the more like it is that it will work its way through and into your basement.
Heavy Rainfall or Groundwater Pressure
Concrete isn’t nearly as impenetrable as it may seem. Given enough pressure, say after particularly heavy rainfall, groundwater will push its way through tiny cracks in the bulkhead walls. This problem is made even worse if there are other weaknesses like poorer seals.
While this can happen to any sunken concrete structure, some types are more vulnerable than others. Cinderblocks, for example, are particularly porous and can become waterlogged.
Bulkhead Repair and Replacement Options
When you’re faced with a leaking basement bulkhead, all is not lost. There are a range of options for repair or, failing that, full replacement. Which makes most sense depends on the problem you’re facing.
Sealing and Surface Repairs
Sealing and surface repairs address external vulnerabilities in your bulkhead, such as worn sealants, porous materials, or degraded mortar, to prevent water infiltration and restore structural soundness.
Resealing a Cinderblock Foundation From The Outside
The nuclear option involves excavating around the walls of your foundation and installing sealants and barriers to block water at source. This is ideal for older cinderblock basement bulkheads and goes a long way in counteracting the inherent problems with porous materials like blockwork.
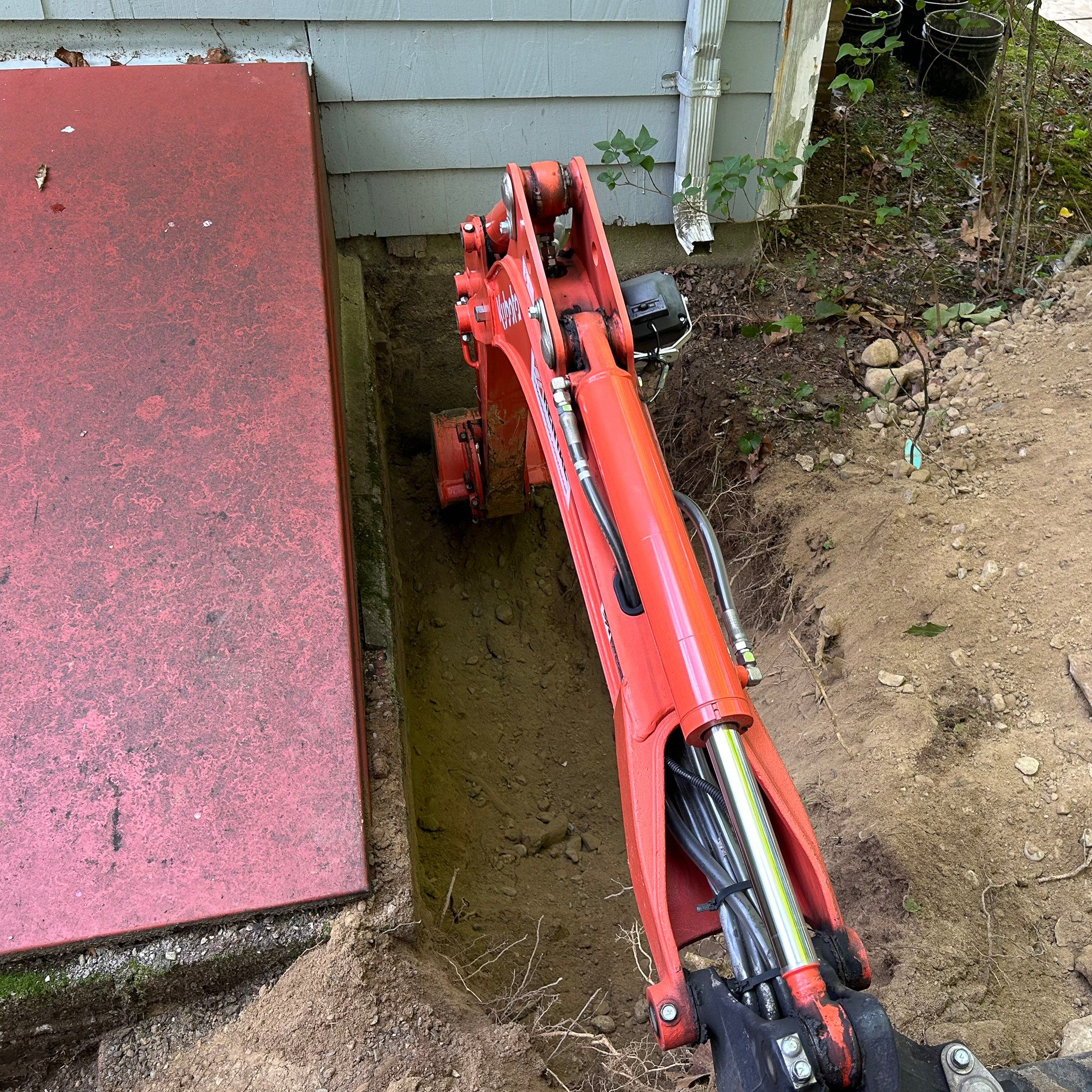
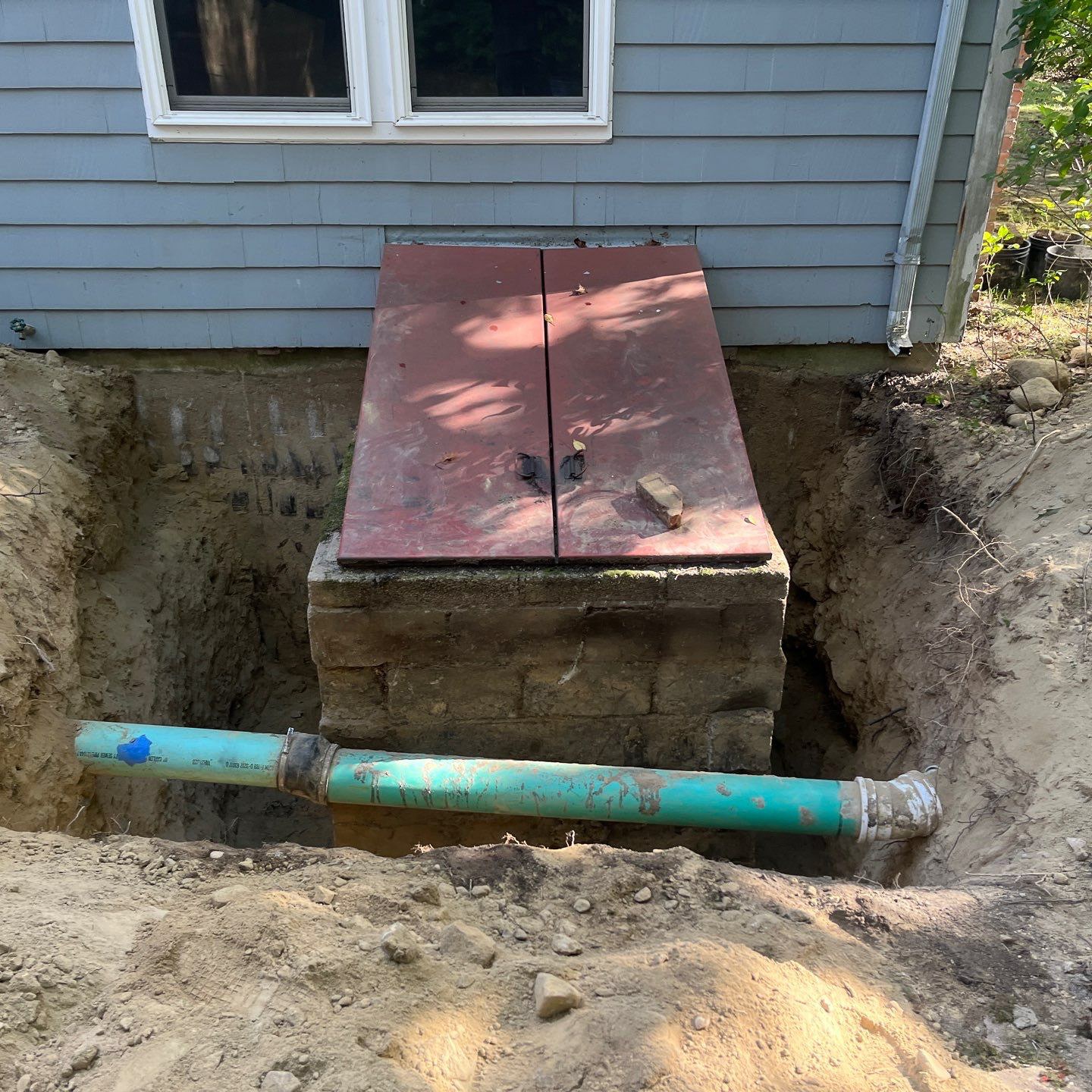
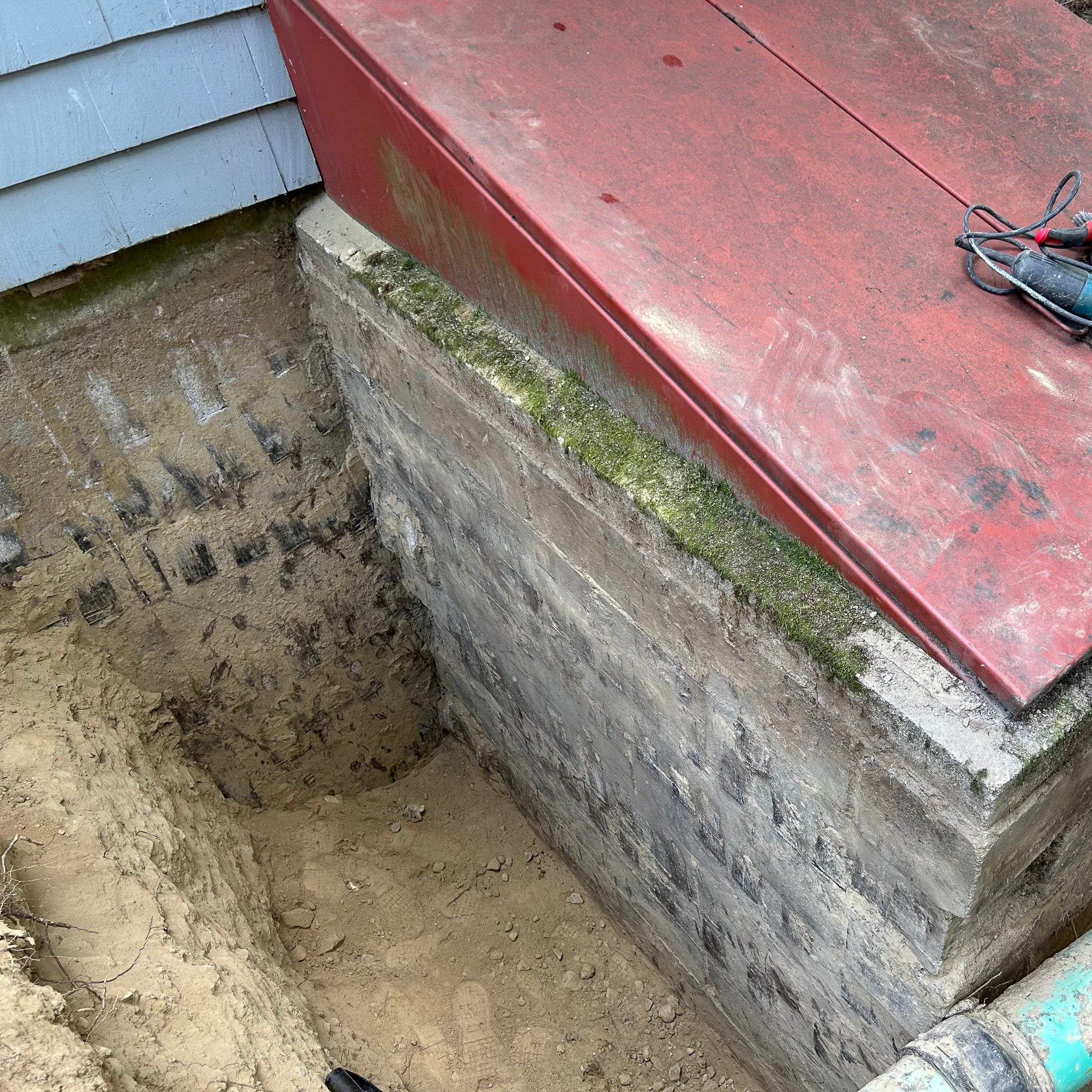
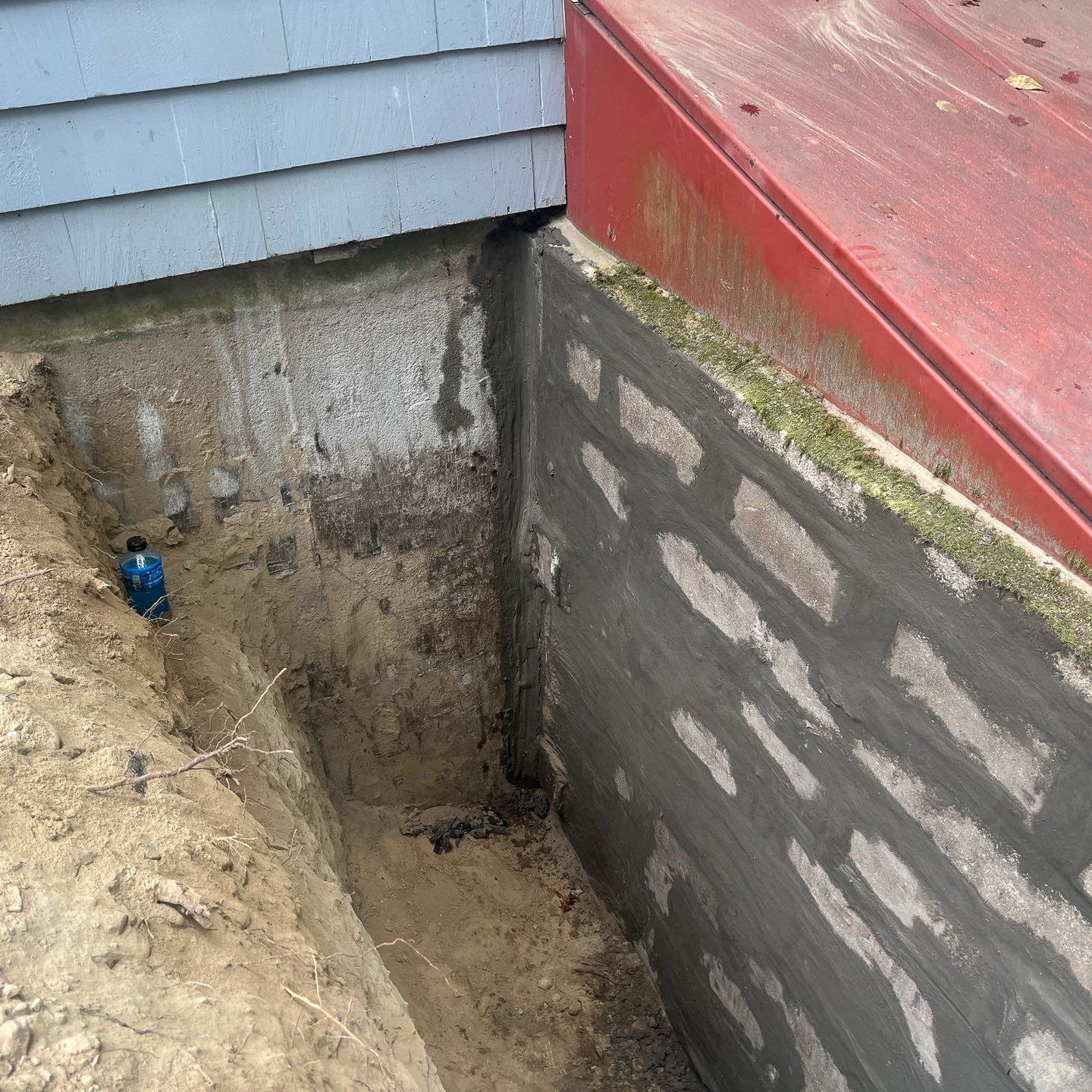
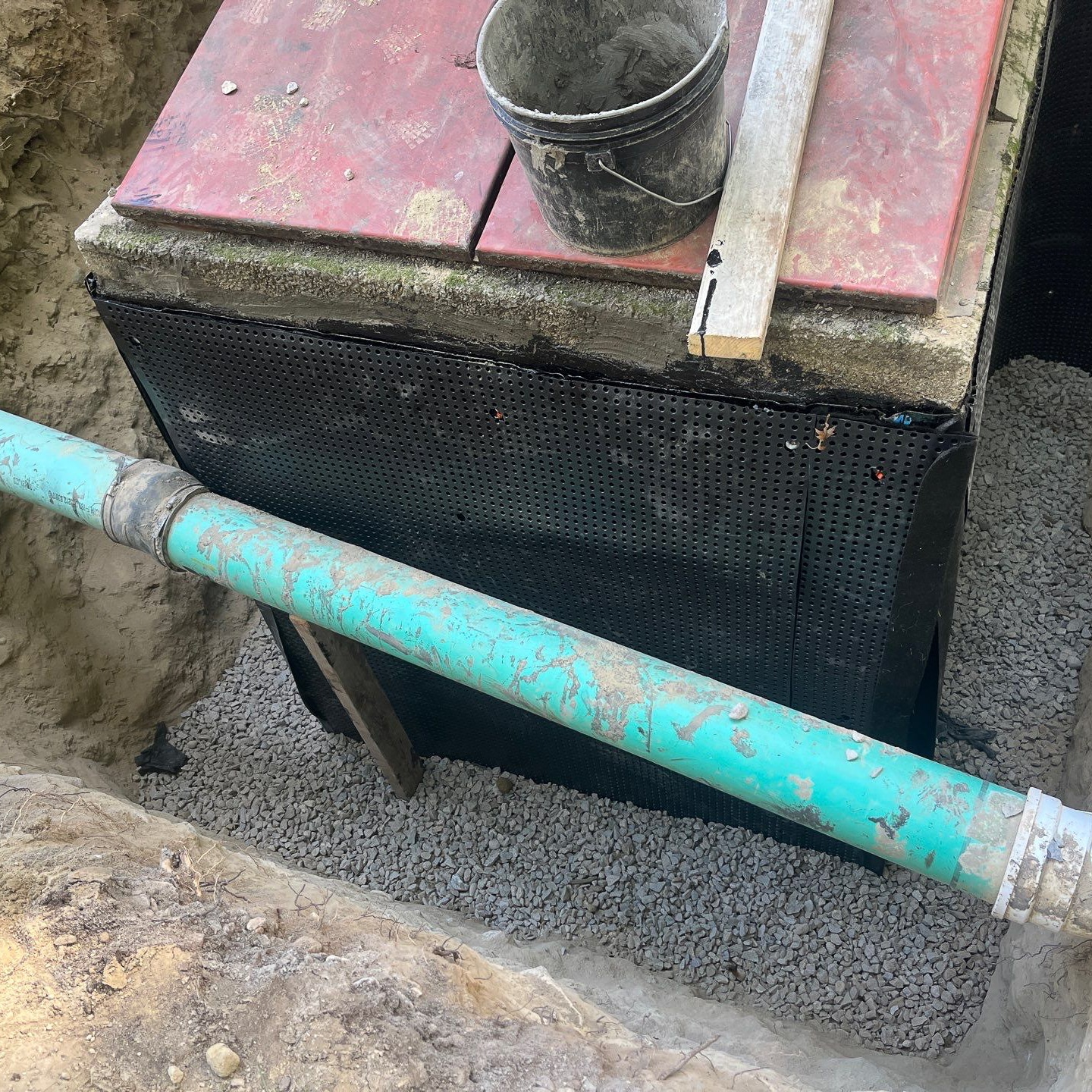
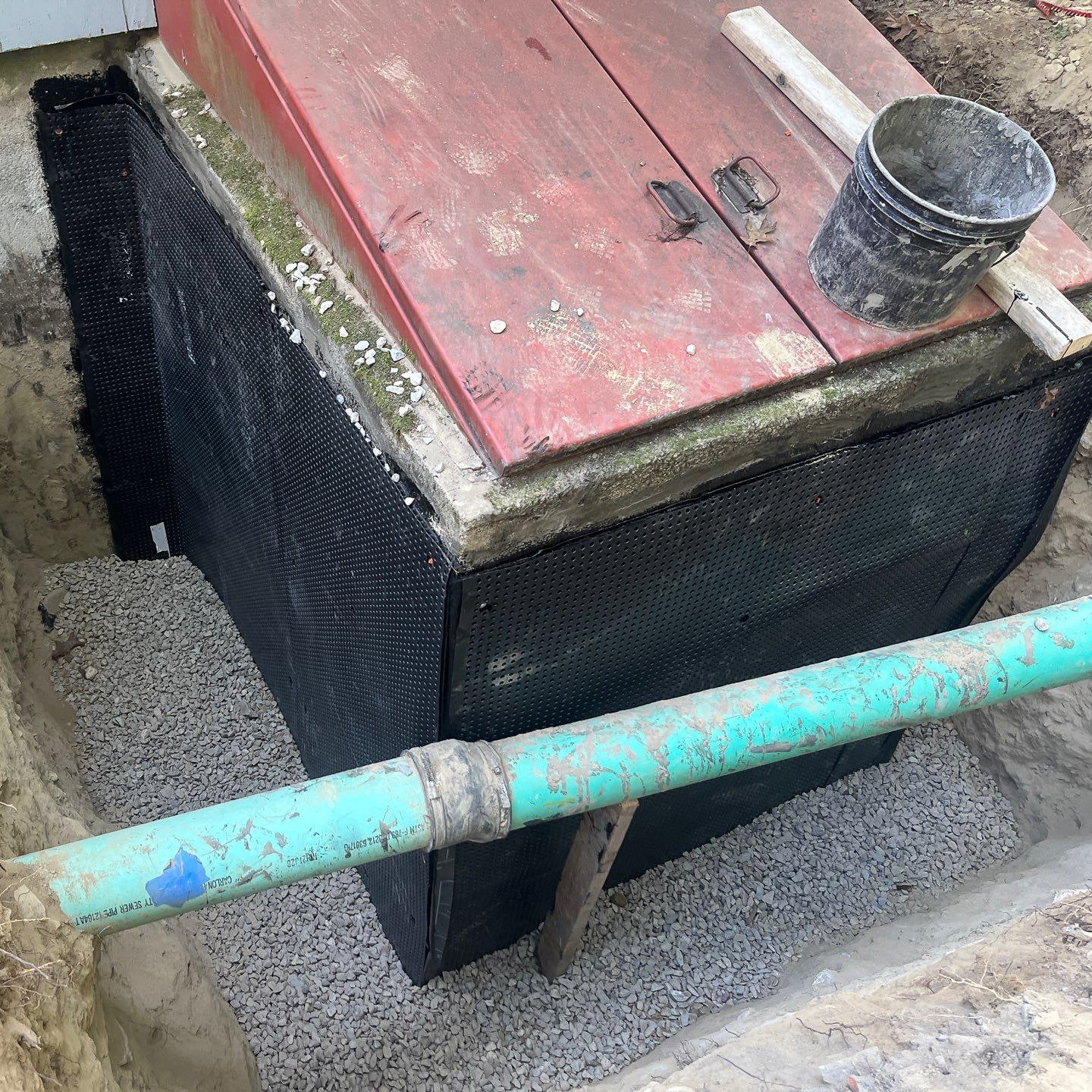
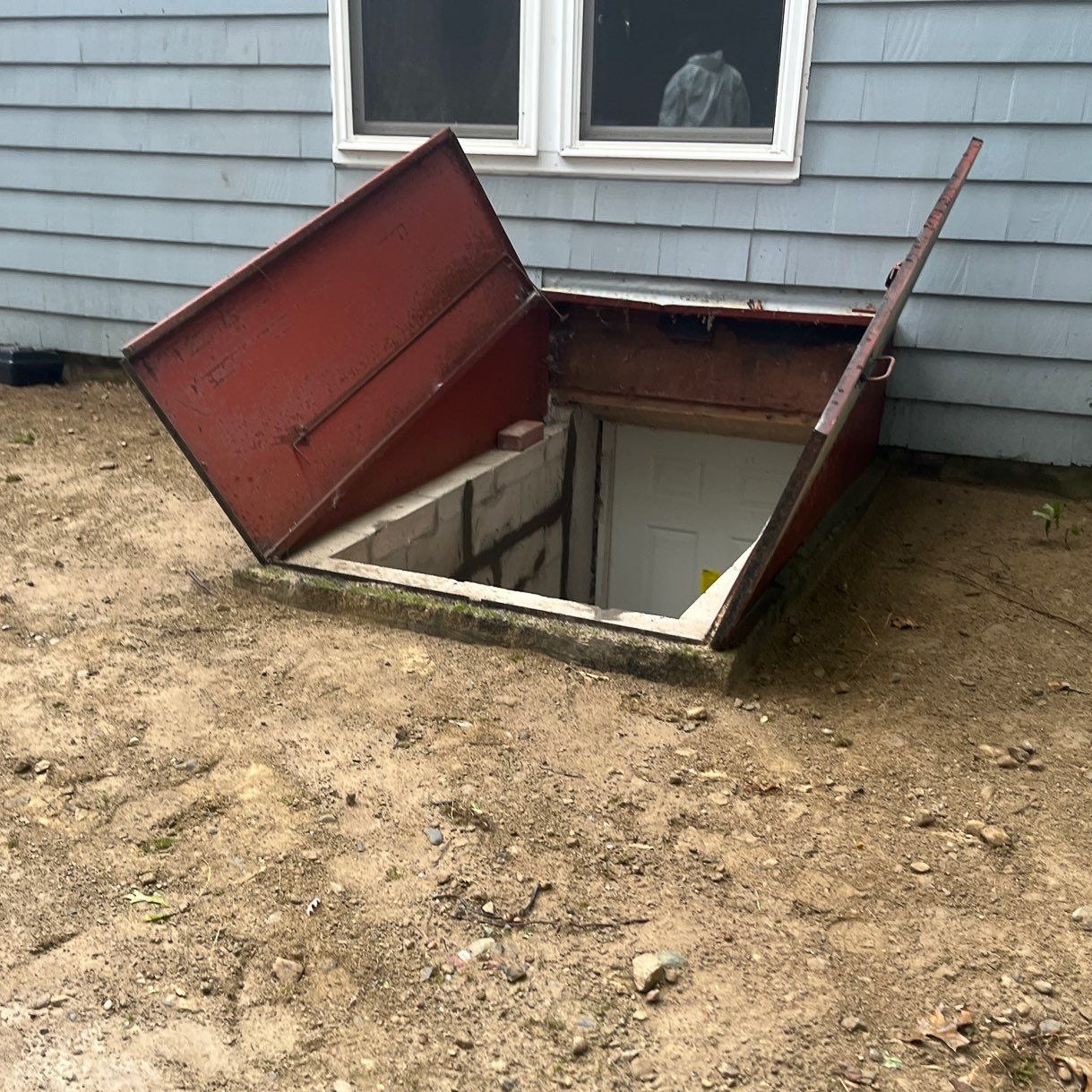
Mortar Repair for Joints
Repointing a blockwork (either brick or cinderblock) bulkhead can repair age related damage. Over time, the mortar which joins the blocks together can erode or crack, creating gaps. Repointing involves chipping this out and replacing it, restoring structural integrity and blocking water.
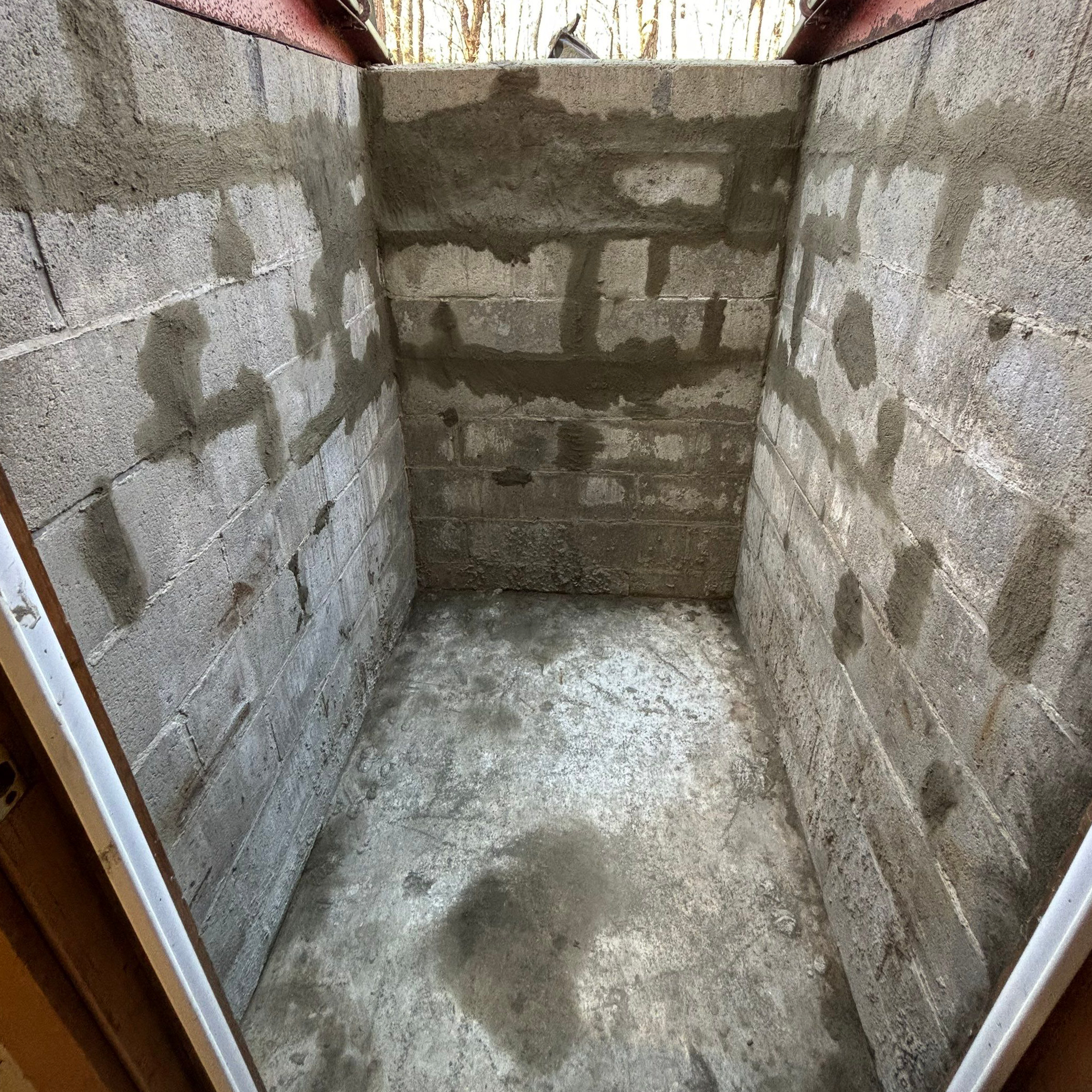
Targeted Crack Repairs
Targeted crack repairs focus on addressing specific cracks or joint issues using advanced injection techniques to create durable, watertight seals and reinforce structural integrity.
Crack Repairs in Precast and Poured Foundations
When faced with visible cracks which are causing leaks and structural vulnerabilities, using epoxy or polyurethane injections can create a watertight seal.
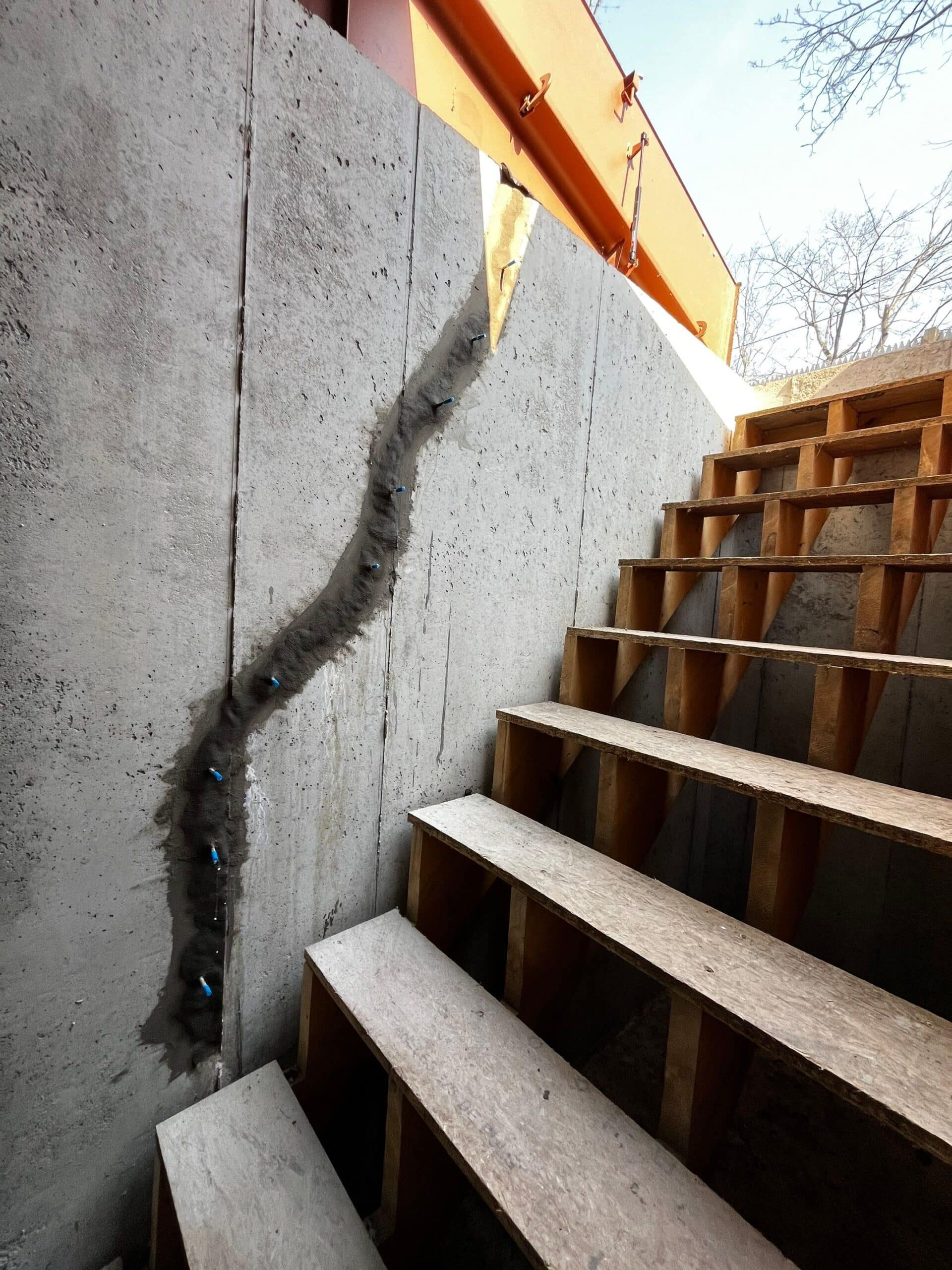
Cold Joint Injection for Precast Foundations
Cold joints in precast bulkheads, such as the seams between the bulkhead components or the connection to the foundation wall, can sometimes develop leaks. To address this, sealants or epoxy can be injected into the joints. This process creates a watertight seal while maintaining the structural flexibility of the bulkhead.
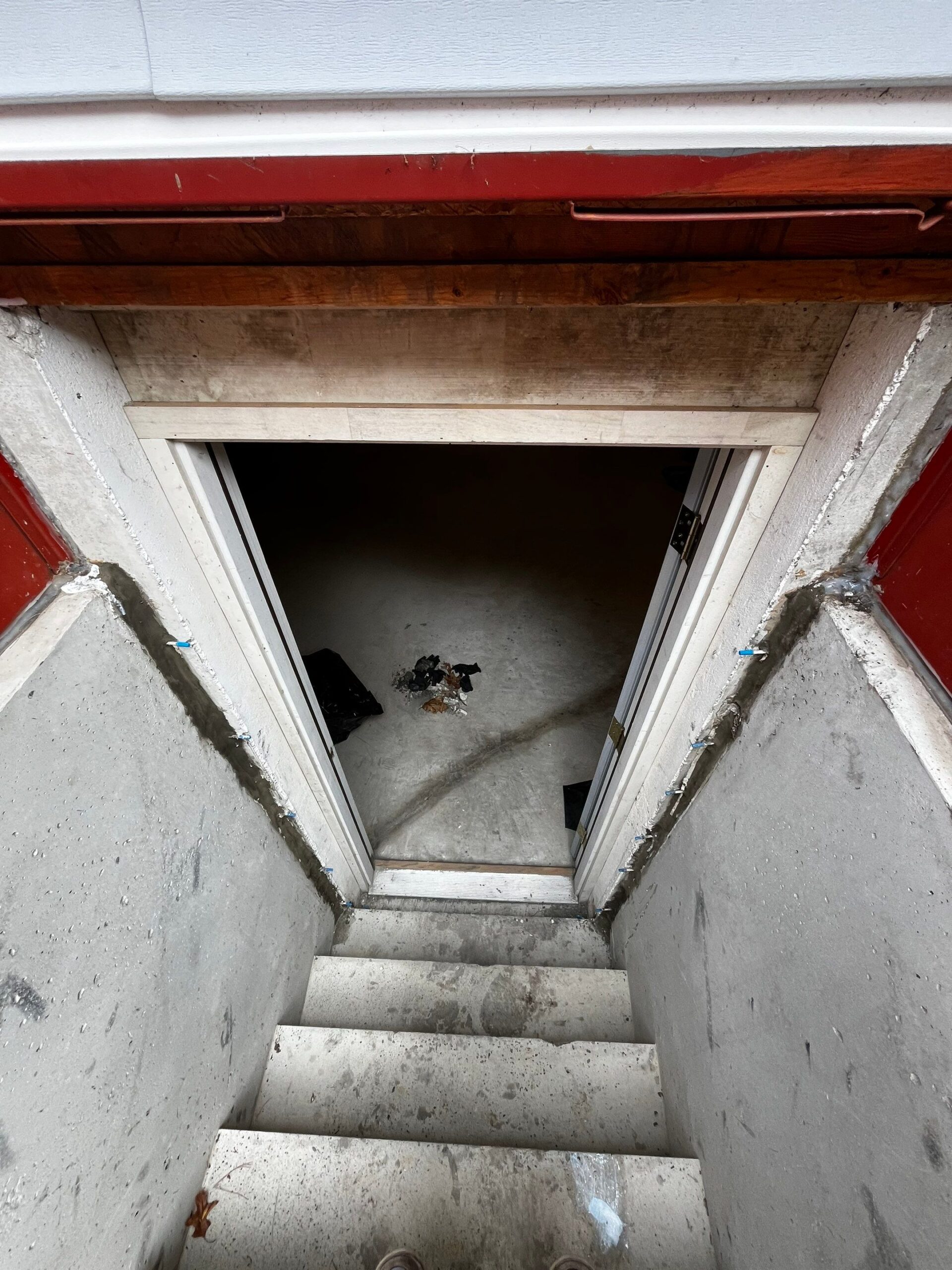
Gate Drain with Sump Pump Integration
Where water run-off is creating a problem, installing a gate drain and tying it into your sump pump may alleviate the issue. As water finds its way into your basement, a gate drain, usually placed at the end of the stairs or under the basement door, catches it. It’s then directed into the sump pump’s pit where it can be moved away without pooling.
This is an ideal solution for properties with poor grading or which are prone to water pooling in the bulkhead.
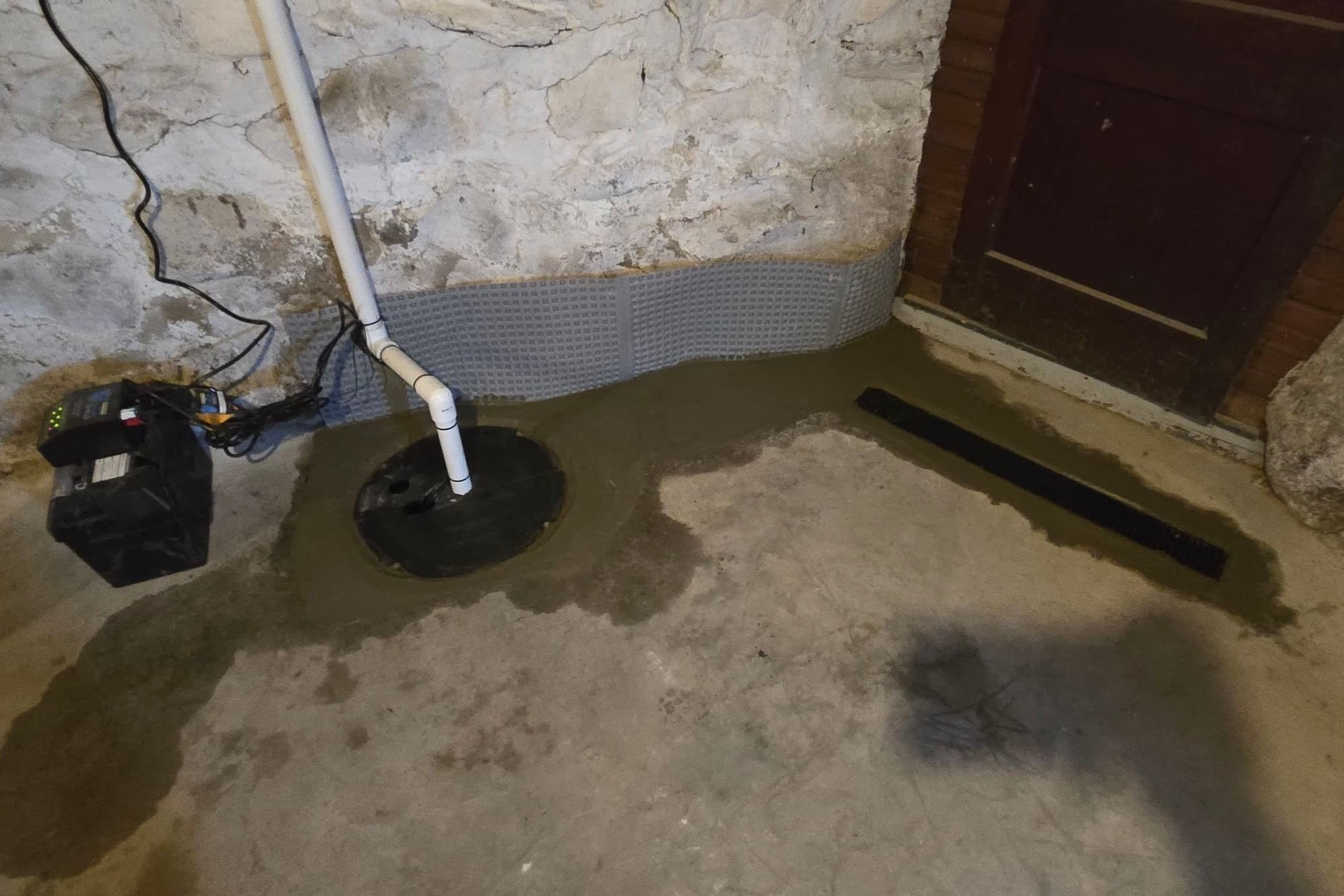
Comprehensive Replacement Options
Sometimes, the best option is to rip it out and start again. Leaking basement bulkhead doors can be replaced or, should it be deemed necessary, the whole structure can be demolished and rebuilt.
Bulkhead Door Replacement
When the structure is sound, but the door has degraded, replacing the door is the obvious choice. This gives the chance for homeowners to ensure that the seals at the connection points are watertight and deals with issues caused by rust, warping or other signs of wear and tear.
If you’re considering replacing your bulkhead doors, it’s worth considering the choice of material. Modern composites and steel are hardwearing and weather-resistant and should last for years.
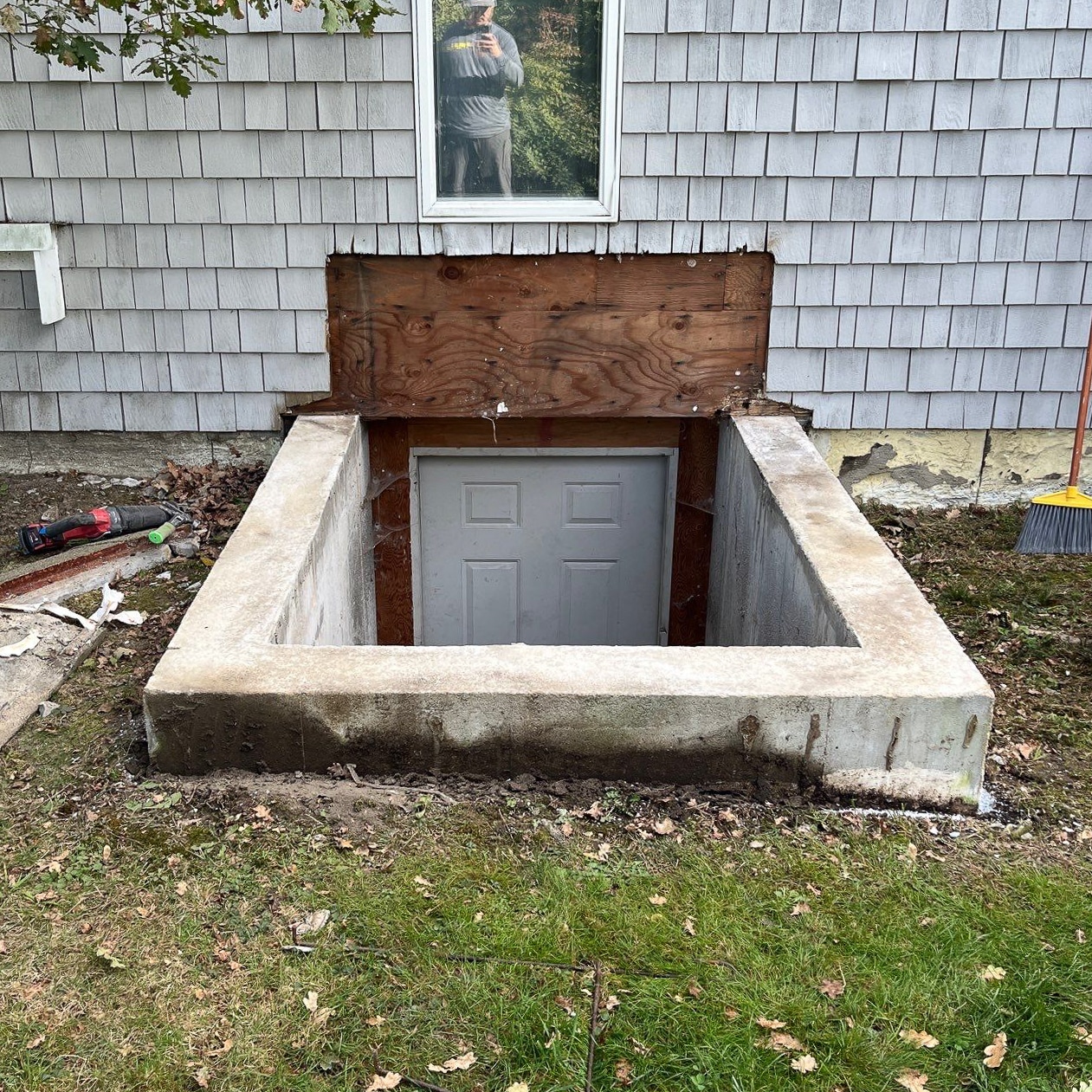
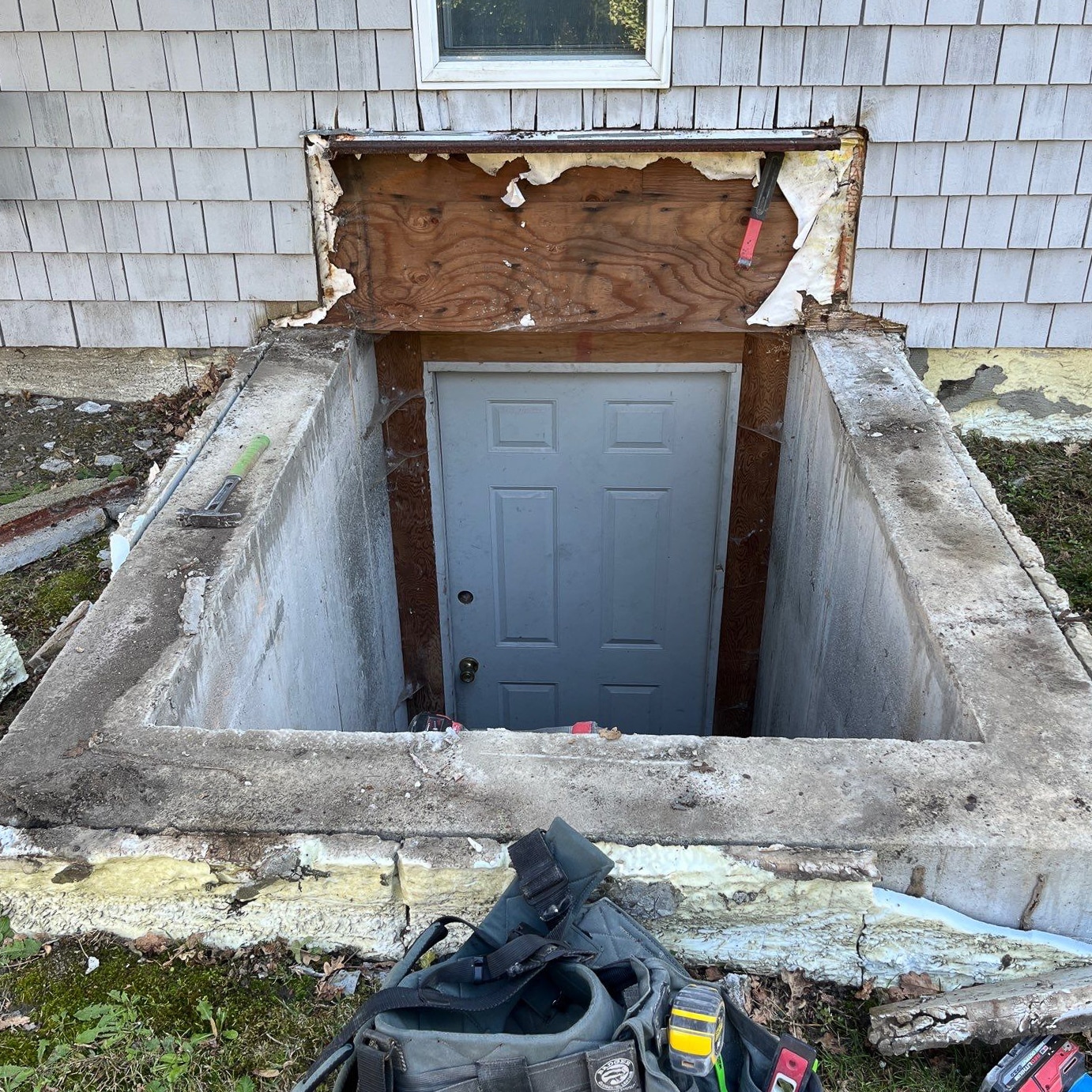
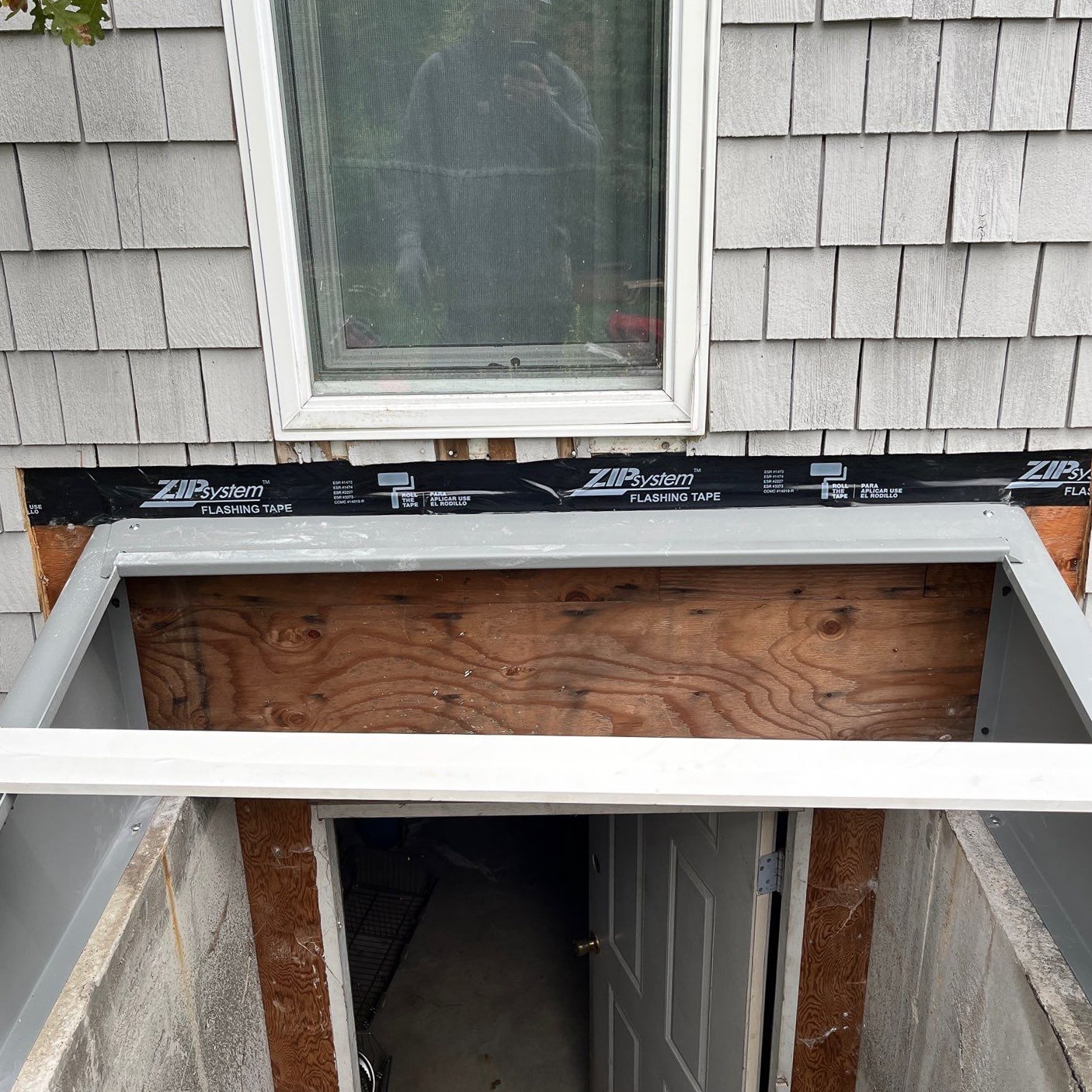
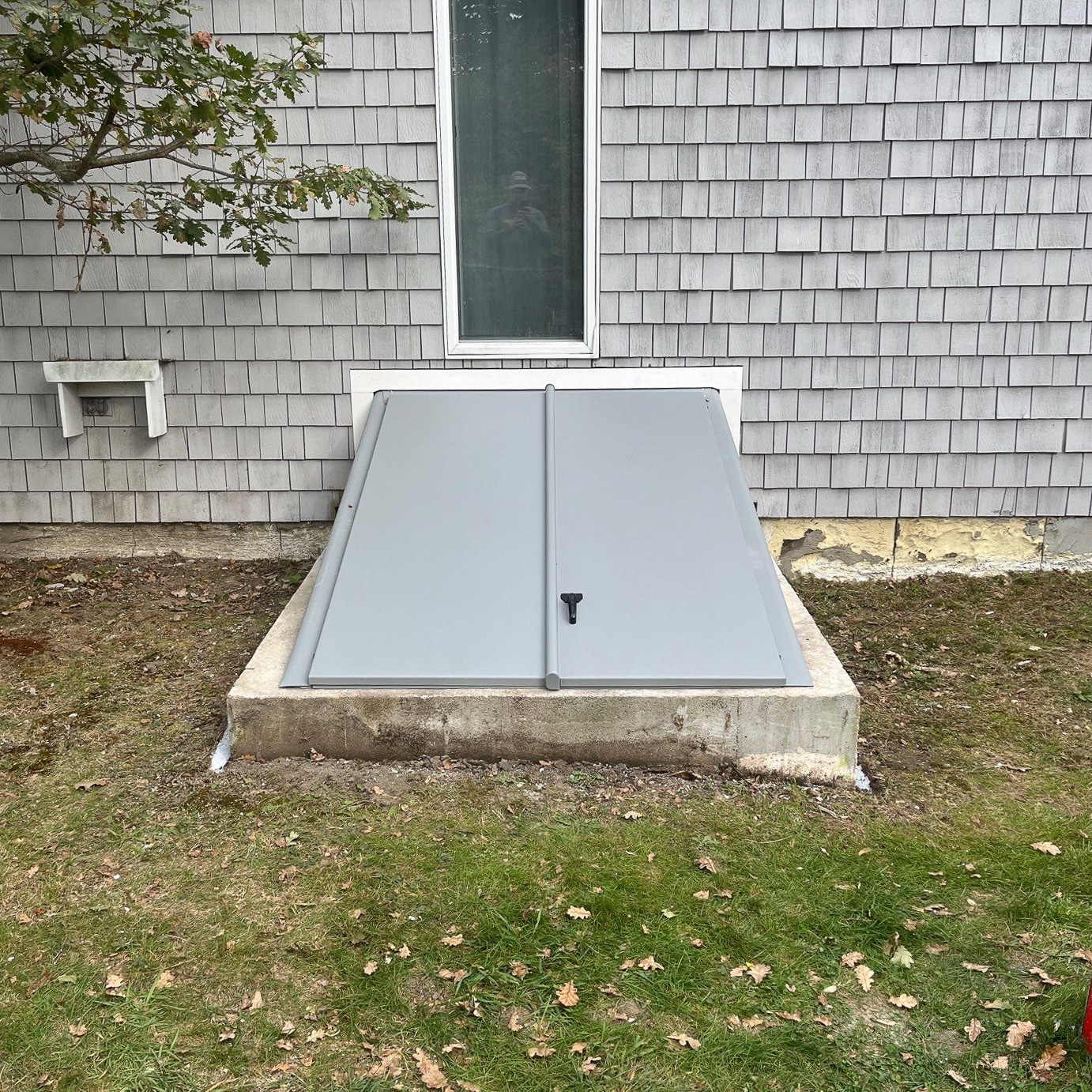

Full Bulkhead Replacement with the Foundation
When things have progressed too far for a simple repair, the only option left which makes sense might be to start over. When the bulkhead is particularly compromised or the foundation is suffering from extensive damage like crumbling cinderblocks or cracking concrete, this might be the most economical choice.
This involves replacing the bulkhead door and the foundation structure with an entirely new version. This offers the chance to sort underlying problems at the same time as upgrading the structure with a new, watertight system.